
Production, packaging and distribution
"The way we brew beer significantly affects the landscape around us. We therefore continue to invest in brewing modernisation to be as nature friendly as possible to our surroundings. We reduce water consumption, minimise our carbon footprint and reuse waste. I am personally pleased to be a member of the team that has managed to achieve excellent results thanks to which we help preserve natural resources for our children. And that is the most important thing for me as a father.”
—Tomáš Kosmák, Investment Manager for CR&SK
We reduce water consumption
One litre of beer requires about three times as much water to make. A few years ago, it was four times as much, and ten years ago, it was even ten times that amount. It is not that so much water evaporates during brewing; water is used to maintain sanitary standards in production for bottle washing and other activities.
WATER CONSUMPTION PER BREWERY
Since 2007, large sums have been invested at all three plants, thanks to which we managed to reduce water consumption to 2.99 hl/hl of beer across the Plzeňský Prazdroj Group.
Most water and electricity are consumed at the brewery in Pilsen, where the legendary Pilsner Urquell is brewed. The reason is that this “legend” has a very demanding production process that uses a great deal of water and energy.
At the Nošovice brewery, we have reduced water consumption to a remarkable 2.51 hl/hl, which is unique worldwide! Our goal for the following years is to bring total water consumption in all our breweries down the rates achieved at the Radegast Brewery in Nošovice.
Average water consumption at all Plzeňský Prazdroj breweries
How have we managed this?
For instance, if hot water is a by-product of brewing beer, we collect it and use it to rinse kegs. Even after the third rinsing of various equipment, the water is still clean enough to be used for the first washing in the following cycle. When we soften water for the brewing process, there is a small amount of very hard water left. This, however, poses no problem for steeping barley in the malthouse, so we use it there. The water evaporated during mashing and boiling hopped wort (about 10 %) is used to produce hot water. The water used as a pressure medium in the pipeline is only partially eliminated. Only the water that was mixed with beer is lost, but the rest is used again.
We have implemented a number of similar measures in recent years. The goal is saving on the input as well as returning as much used liquid back to the process as possible. Of course, that is only possible if its quality allows us to do so. We have and continue to develop monitoring systems which optimise our consumption. Each and every employee is trained in resource conservation. We recently commenced a project to optimise our sanitation processes and the project will continue into 2019 with further water consumption reductions anticipated.
We reduce energy consumption
Saving energy in a Czech brewery is almost a Sisyphean task if the production is to be done properly, as Czech beer requires a great deal of energy. Genuine Pilsner lager requires triple mashing. The processes of wort boiling in the brewhouse and beer maturing in lager tanks are long and thorough, and the lager tanks must naturally be thermoregulated as well.
Although our goal is to reduce the energy consumption of our production, we recorded a slight increase in energy use in the last year. In 2018, we achieved total direct energy consumption of 81.60 MJ/hl. That is 0.12 MJ/hl more than in 2017. The main reason was the increased production of popular Pilsner Urquell.
Nevertheless, our total energy consumption has been decreasing in the long run – by a remarkable 42% in the past decade.
Total Direct Energy
How was this achieved?
We have achieved this mostly by energy recovery, the thermal insulation of buildings, lighting replacement (installing LEDs), boiler renovations and production optimisation. We monitor energy consumption and the effectiveness of the measures on a weekly basis.
Reducing our carbon footprint
Every human activity contributes to the greenhouse effect. So you can keep enjoying beer, we are tackling our carbon footprint among other things by optimising production and distribution and investing in our fleet.
Carbon efficiency has improved by nearly 20% in the past 4 years.
efficiency
kgCO2/hl
Our commitment is a further reduction in our carbon footprint per one litre of beer by 1/3 by 2021 compared to 2016. This is the goal for the whole Asahi Breweries Europe Group.
Streamlining distribution
We streamline our distribution
Producing and getting our products to customers requires a lot of energy, the result of which is the release of carbon into the atmosphere. This is why we demand good environmental behaviour from our suppliers and, at the same time, address our own distribution.
So, what do we do?
We have launched a new system of beer distribution to tank pubs. We have increased the volume of beer transported in mobile 5 hl tanks. Compared to 2017, when we distributed 9,000 hl in mobile tanks, the new transport system has significantly increased their turnover, and the extension of their number by another 80 units helped us manage the transport of 45,000 hl of beer in them in 2018. This resulted in a reduction of the distance covered by tank beer transport by 271,000 km!!! We expect a further decrease of mileage needed for the distribution of one hectolitre of tank beer by another 26% in the following year. In addition, 80% of the existing fleet distributing tank beer meets the EURO 6 standard.
In 2018, we purchased 20 new tandem trains with fuel consumption reduced by 10%. They will be introduced into distribution beginning in January 2020.
In March we launched the operation of a train connection between Pilsen and Nošovice, transporting beer as well as packaging materials between our breweries. That has removed 416 trucks from Czech roads and motorways.
We also influence the effectiveness of distribution by means of competitions and training courses for drivers aimed at reduced vehicle wear, lower fuel consumption and a more environmentally-friendly driving style.
We are not afraid to experiment and introduce new technologies in our distribution network. In November 2018, we tested our first electric truck in operation. Unfortunately, the tested truck was unable to meet our expectations, especially the distance covered per single charge.
Reusable bottles? There is nothing better than that...
All our packaging is100% recyclable. We reduce our carbon footprint and quantities of packaging waste by our transition from keg beer to tank beer in pubs and restaurants.
A tank is simply more efficient than a truck and, moreover, tank beer has an exceptional taste.
Unfortunately, in recent years store demand for beer has been increasing at the expense of pubs and restaurants. This is reflected in increased interest in containers convenient for consumers – PET bottles and aluminium cans. Therefore, the proportion of our products in returnable packaging has decreased slightly – by 2% compared to 2017.
We distribute 67.65% of our beverage volume in returnable packaging
Waste or material that can be reused?
Part of our sustainable development strategy is to achieve operation with zero waste. Although this task appears unachievable, we are slowly approach our goal. Nearly 98% of all waste generated by all Plzeňský Prazdroj breweries and the commercial distribution centres is recycled. In 2018, this quantity was just slightly less, by only 0.5%.
Waste generation at Plzeňský Prazdroj in 2018
Total waste production 183,272 tonnes
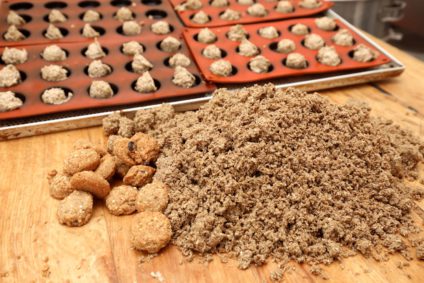
An overwhelming majority of our waste is of organic origin and is therefore used as a secondary raw material as much as possible.
We supply spent grains to farmers or for green energy generation. Yeast and waste malt are used as feed. Treatment plant sludge is used as soil fertiliser. Diatomaceous earth from waste filtration is used to lighten soil in recovered areas. And the rest of our waste is carefully sorted.
Last year we were inspired by circular economy principles in the preparation of an untraditional experiment with spent grains. Spent grains are used malt resulting from brewing. Their composition is rich in protein and fibre and low in sugar. It would be a real shame not to use such properties! That is why we addressed the Organic Bakery Zemanka, inviting them to join our project and develop a product from our spent grains. The experiment resulted in excellent biscuits that are ideal with beer. This one-off experiment was not aimed at large-volume biscuit production, at least for the time being. And if we decide for biscuit production in future, we will only use a small fragment of the total quantity of spent grains available. Our effort is mainly to show that even waste can be used for the production of products with added value.
Do you know what we do with labels?
Cleaning beer bottles produces tonnes of used labels. What to do with them?
A couple of years ago, Radegast began to supply them to a compost plant, in a quantity of around 400 tonnes per year. The labels are mixed with wastewater sludge, landscaping waste, etc. After 90 days, a substrate is produced that is usable for paving roads or dump remediation.
Certificates
In 2018, we successfully passed certification audits of our integrated management system. The scope of the audits included our production plants as well as distribution centres and technical service units. We now hold the following certifications:
Our activities help fulfil the following goals of sustainable development: